Every multifamily project is designed with our BIM software by a team of designers who primarily have had extensive experience working as carpenters. Each contracted project has a salaried team assigned consisting of:
- Project Manager
- Lead BIM designer
- Field Superintendent
- Pick up foreman
- Team production lead’s for framing, joisting and sheeting
- All of our management and design teams are English speaking
Design Method
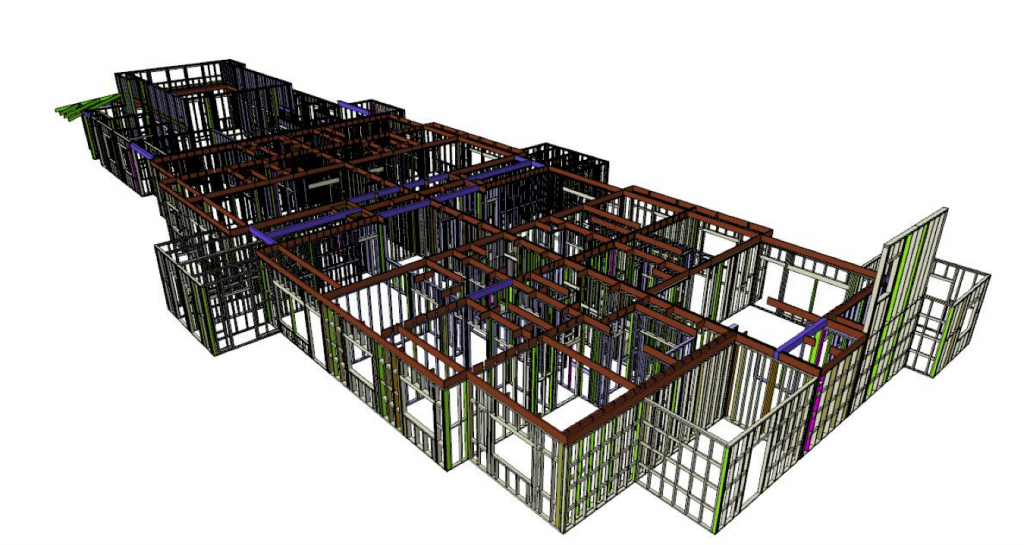
We use a BIM (Building Information Modeling) environment to model and coordinate rough framing issues such as: architectural requirements vs. structural, plumbing, HVAC, and electrical.
Using BIM, up to 95% of the framing issues can be resolved. After which, we can then build the major structural framing components at our off site facility.
- Vetting majority of the issues prior to construction.
- Team interacts in advance during cooperation process.
- Coordinated model is utilized in the field directly.
- Coordination process potentially saves time on critical path and schedule.
- Cost savings related to future CO reduction.
Framing Methods
SPEEDY-FRAME™
- BIM design & Coordination
- Laser edge plate layout
- Precision trim components
- Walls manufactured on-site
Good for sites that have certain restrictions or environmental challenges.
PANELIZATION
- BIM design & Coordination
- Laser edge plate layout
- Precision trim components
- Walls manufactured off-site
Consistent layout and framing unit to unit and floor to floor. Significant time saving on critical path.